Motivations
In the melting area of steelworks situation awareness is a key to ensure process reliability, health and safety at the workplace and low environmental impact.
The hemorrhage of highly skilled people in a sort of ‘war of talents’ is a serious business threat, which can be faced by creating attractive workplaces and stimulating working conditions;
The steel industry workforce is undergoing an unprecedented change: more than 30% of the workforce is leaving the sector in the period 2015-2030, with a relevant loss of expertise, hard to timely re-form using traditional means and strategies.
On the other hand, the ongoing “digital transition” also provide relevant opportunities:
- Novel sensing devices are now available also suitable to the harsh environmental conditions commonly found in the melting area.
- Artificial Intelligence and Machine Learning enable processing and interpretation of large volumes of heterogeneous data.
- New generations are familiar with training and learning solutions based on simulation tools.
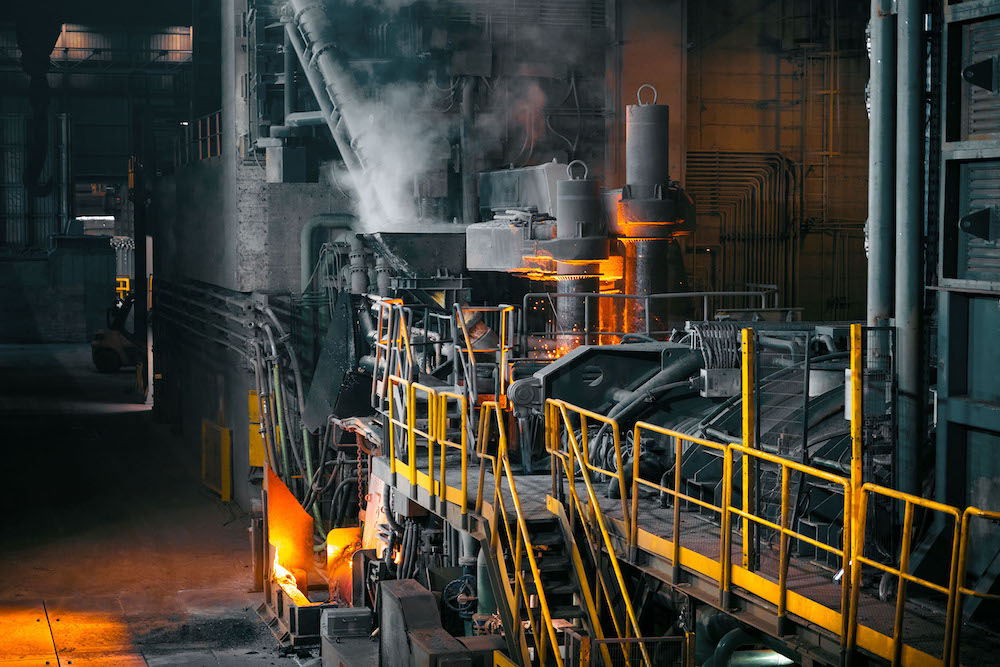
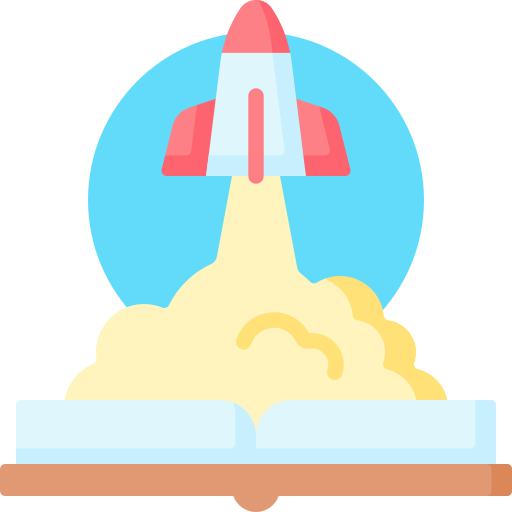
Mission
iSteel-Expert implements and demonstrates in industrial environment a remote expert virtual system that monitors 24/7 the progress of the process, analyses the information and suggests actions to improve and/or correct steelmaking operations.
iSteel-Expert acts as a human expert in collecting and analysing information from the furnace, substantially increases its quality to support operators in maintenance and decision-making. Based on IoT, it enhances human management capabilities, timely detects relevant events, and identifies their consequences.
A knowledge-based approach is integrated in an interactive immersive training tool, which favours preservation, transfer, and continuous evolution of the company’s wealth of knowledge.
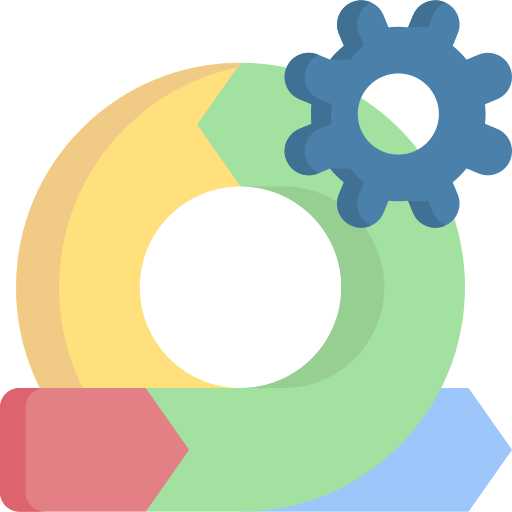
Methods
Our methodology is based on five fundamental pillars:
- Ad-hoc installation of commercial sensors suitable to the harsh steelmaking environment.
- Dedicated data collector electronic board to simultaneously collect plant data in different formats and types
- local preprocessing station for video, acoustic, vibrational and temperature data, to extract relevant features and to transfer only necessary data to a cloud infrastructure.
- Cloud infrastructure running sophisticated algorithms (including Machine Learning) to provide useful Key Performance Indicators and smart information via user-friendly and effective dashboards on a dedicated WEB portal.
- Interactive immersive simulation training tool using raw and processed data and exploiting innovative approaches.
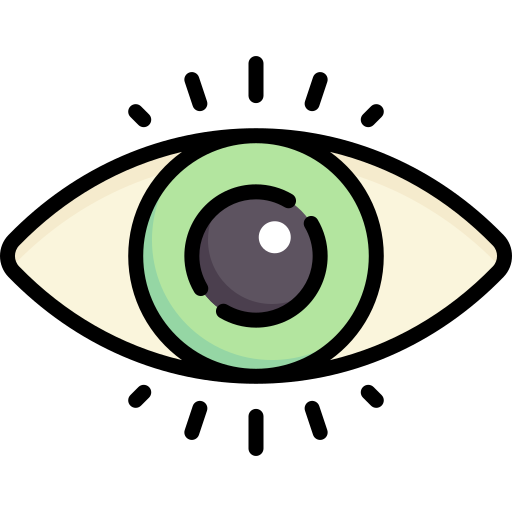